A durable dock requires high-quality materials to withstand the waterfront environment. Choose pressure-treated wood or composite decking that resists rot, rust, and pests. Galvanized steel hardware offers corrosion resistance in saltwater.
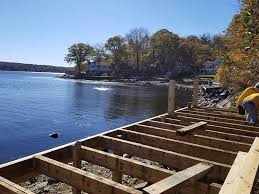
Understanding the stability of the lake bottom helps determine pile type and length. Piles must transfer expected and unforeseen loads through the lakebed to more stable soil or rock layers below. Keep reading the article below to learn more about Dock Construction.
A dock is a structure that connects a boat to land and serves as an access point for people to enter and exit the water. It is an integral component of a waterfront property and must be well-designed to meet the specific needs of the users. A poorly designed dock can result in safety hazards, poor performance, and costly maintenance. Several factors influence the design of a dock, including location, materials, and structure.
Local, state, and federal regulations govern a variety of aspects of dock construction, from zoning and coastal management to building standards and safety protocols. A thorough review of these requirements before construction begins ensures that all necessary permits are in place and minimizes the risk of delays or costly modifications during the project.
Load capacity is an essential element of dock construction that must be accurately assessed and accounted for in the design process. A dock that can’t support the weight of docked boats risks structural failure and accidents. A comprehensive load assessment starts with determining the overall weight of the dock, then adding the weight of each watercraft that will be docked there. This is critical to the durability of any dock and ensuring that it will be safe for recreational use.
Residential Users
A well-designed residential dock can add functionality and beauty to a waterfront home. It may include features like boat lifts and ramps to facilitate loading and unloading. It can also include seating areas to accommodate guests and social gatherings. Other amenities like swimming ladders and fishing stations support a wide range of leisure activities.
Commercial or Industrial Needs
A dock for a marina or industrial property requires a more durable and functional design than a private residential dock. It must support multiple launches for watercrafts and be able to withstand heavy loads of equipment and passengers. It also requires efficient layout to maximize productivity and ease of operation for dock workers.
A marine contractor should have the experience and expertise to provide a detailed design that will perform under a variety of environmental conditions. For example, a floating dock would not be appropriate in a region with frequent high winds or currents, and a fixed dock with pilings would not work in a location that experiences flooding events.
Materials
When building a dock, it’s important to choose the right materials that will last. This will depend on the type of dock, your local climatic conditions and other factors.
For example, if you live in an area that experiences frequent storms with high winds, you’ll want to select a strong material like galvanized steel or concrete that can withstand the elements. If your area is prone to a lot of boat traffic, it’s also important to consider the types and sizes of boats that will be using your dock.
Some of the most popular options for boat dock construction include aluminum, wood and plastic. Each has its own benefits and drawbacks. For example, aluminum is lightweight, making it easy to transport and install. However, it can get hot in the sun and may require extra maintenance to prevent rusting. Wood is affordable and durable but can rot, warp or crack over time. Composites and wood-based materials are also prone to mold and mildew growth.
Finally, plastic is a versatile option that is easy to maintain. It can be built to accommodate a variety of water levels and comes in a wide range of colors and textures. It’s also one of the most economical choices for a floating dock. However, it’s not as strong as aluminum or wood and is prone to damage from impacts and rough weather conditions.
The material chosen to build the decking of your dock is also crucial. This will depend on your personal preferences, the size of your dock and how it will be used. Natural woods are the traditional choice for many homeowners, and they can look beautiful and add to the waterfront scenery. However, it’s important to note that wood is prone to rotting, warping and insect infestation. In addition, you’ll need to treat your wood with a waterproofing sealant and stain to protect it from the harsh elements.
For a long-lasting solution, you can opt for a plastic or concrete dock. These types of docks are more resistant to rotting, corrosion and marine pests. They’re also less prone to impact damage from boat trailers and other equipment. For an added layer of protection, you can also choose to install piling sleeves. These sleeves are heat-shrunk onto the piles before they’re put in the water and provide a waterproof, UV-resistant barrier that is resistant to marine pests.
Installation
Effective dock foundations are critical to structural integrity and durability. Tolerances in pile placement and alignment require meticulous planning, precise execution, and stringent quality and safety protocols. These factors contribute to optimal load transfer and minimize the risk of localized failures that might compromise a dock’s long-term performance.
To begin construction, the ground needs to be cleared and prepared for the structure’s footings. This includes removing debris, clearing rocks and other obstructions, and leveling the area where the dock will sit. Then the concrete or welded steel footers are placed. Once the footers are in place it’s time to build the dock’s frame. Once the frame is erected it’s time to add the decking material and attach the shoreline support posts. Lastly, the gangway and accessories can be added.
A dock is more than just a structure that connects people to the water, it’s a functional and aesthetically-pleasing waterfront accessory. The superstructure of a dock directly interfaces with users and vessels, and its construction contributes to operational efficiency, safety, and durability.
To ensure this, dock construction requires a comprehensive pre-construction phase that starts well before the first pile is driven. Geotechnical investigations and hydrodynamic studies help understand the site conditions and load-bearing capacity of the soils and rock layers that will support the superstructure. Environmental assessments identify potential impacts on unique marine habitats and help to develop mitigation strategies that minimize ecological disruption.
Pile systems are the backbone of a dock, and they are designed to transfer forces generated by waves, currents, and operational impacts to the bedrock or soil underneath. To achieve this, piling contractors must have a high level of technical expertise and practical experience in choosing the right pile type and driving technique for the specific site conditions. This ensures that the pile system will be capable of achieving the expected loads with minimal structural and environmental impact.
During the permitting process, municipal, county, and state bodies must review and approve construction activities. This can be a lengthy and time-consuming process that requires the support of knowledgeable professionals familiar with the requirements and regulations. Once construction is underway, a comprehensive budget must be developed to account for the initial costs as well as anticipated maintenance, repair, and upgrades over the dock’s lifespan.
Maintenance
A dock is a significant investment and its longevity is directly related to how well it’s maintained over time. Regular safety and quality inspections will identify issues and allow them to be addressed quickly, minimizing deterioration and costly repairs. Regular cleanings and coatings with corrosion-resistant materials will extend the life of a dock, protecting it from water damage, UV rays, and debris buildup.
A properly functioning dock keeps products flowing smoothly in and out of a warehouse, minimizes the risk of workplace accidents, and keeps unwanted pests and debris from entering a facility. Unfortunately, many companies overlook dock maintenance and are left scrambling to find a solution when the system breaks down. This costs money, productivity, and even workman’s compensation claims.
Whether you have a residential or commercial property, your dock is an important part of the overall appeal and value of your waterfront property. A pristine, well-maintained dock will make your property more appealing to potential buyers and tenants. It will also help protect your property from environmental damage, such as erosion and ice damage.
Residential dock construction requires specialized engineering to handle heavy loads and resist corrosion. This is especially true for docks located in coastal regions, where exposure to saltwater and fluctuating weather conditions can cause rapid deterioration. High-quality materials, a skilled installation team, and a strong warranty will provide long-term durability.
Industrial docks are designed to support large, heavy-duty vessels. They often feature loading/unloading bays, cargo elevators, and storage sheds. These structures must be built to withstand severe storms, winds, waves, and other natural hazards. They are also prone to ice damage and must be constructed from durable, low-maintenance materials.
A successful dock construction project requires a thorough permitting process. This includes obtaining approval from the local, county, and state levels. It also includes an environmental impact assessment, which is vital to preserving unique ecosystems. A professional experienced in the permitting process can guide you through this time-consuming and complex stage of a commercial dock construction project. They can also recommend mitigation measures, such as silt curtains, to minimize sediment disruption during construction.